I consider each mouthpiece a real art work, I play and watch it carefully until the mouthpiece suggest me where to go, what aspects changed to achieve an excellent result. Precisely for this reason that two blanks not will lead to two identical mouthpieces, as two mouthpieces are not identical in form or sound, each one is unique and inimitable.
I do not rely too much on measures of scanners or CNC machines, but I focus my mind to the objective results that are perceived as the piece is changed: I’m a clarinetist and therefore I play, work and re-play each mouthpiece until reach the desired goal. Sometimes, to be able to fully meet the expectations of the musician I change my way of playing based on the style, the posture and the material that uses the clarinetist I work with at the time.
My idea is to accompany the artist along its path of sound development, allowing them to have a comfortable mouthpiece that allows them to give their best, unimpeded, sing happy and satisfied with the quality and the sound of their control .
The hand-finished neck are not a fad of the moment, in the past all played it until the arrival of modern production technologies. The industrialization has speeded up the production, unfortunately at the expense of quality. The main reason is obvious to all, “the machine can not play”; it is impossible to arrive at a balanced mouthpiece in all its forms and features without trying, without playing it. No machine can achieve the skill of a craftsman, both for the extremely complex shape that for the multiple proportions of infinitesimal measures (0.001 mm).
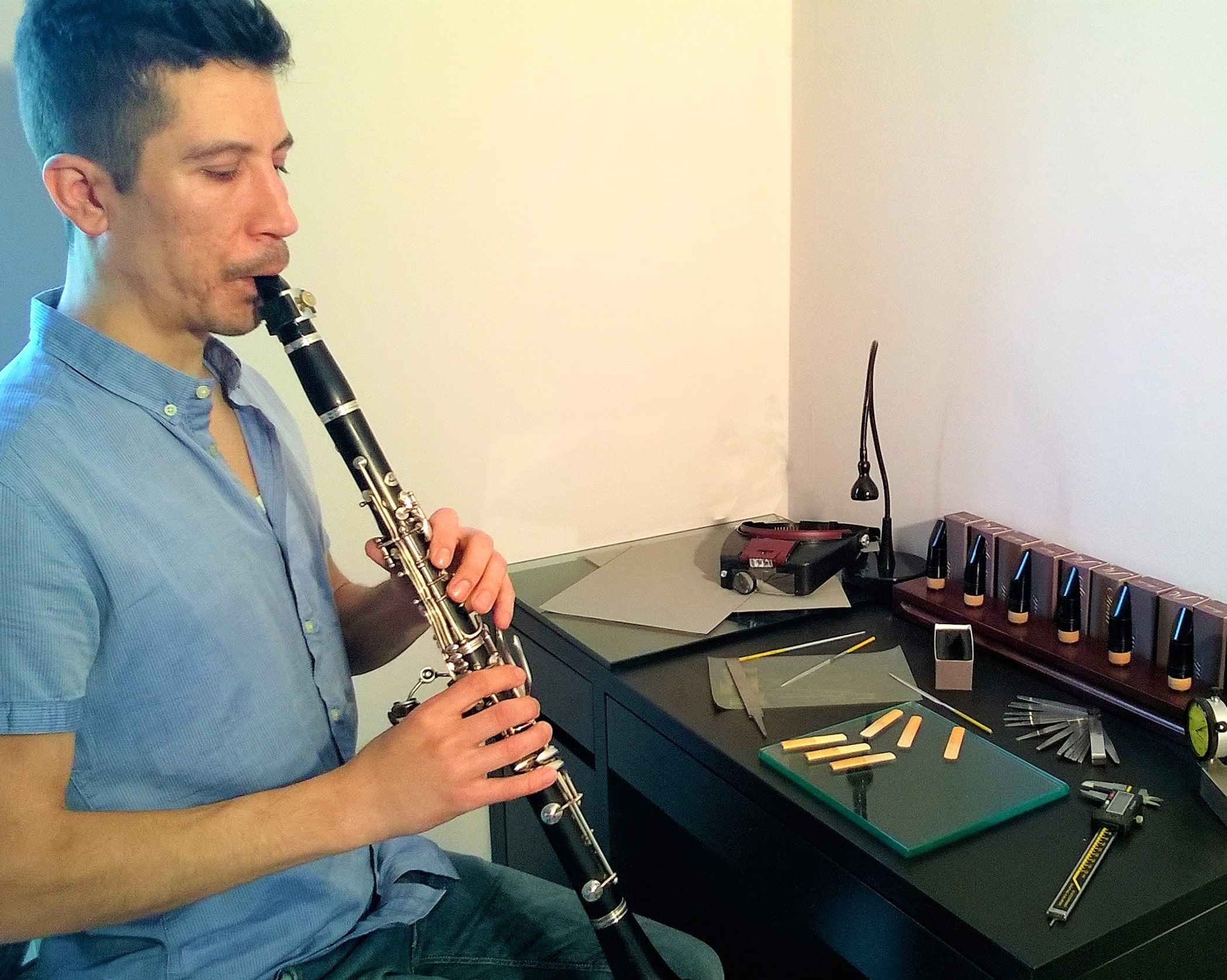
"... The sound of the clarinet even in extra soft floated above the orchestra coming sharp and at the same intense way is last in the audience that high in the gallery ..."
These are phrases that from when I was child impressed me. We all have heard and read that clarinetists in the early twentieth century, with the limiting materials, in the absence of technology, were able to have great projection with exceptional sounds in timbre and color.
I studied techniques and forms adopted by the best craftsmen in the past, I tried to capture the details that gradually, over the course of the century, accompanying the evolution of the mouthpieces, the new abandoned to facilitate and speed up production conditioned by the use of machinery or to facilitate the setting and the clarinet approach; As we know, however, simplify, facilitate the instrumentalist too is inconsistent with the opportunity to get a rich sound, burnished with weight. Other good ideas in the past were not adopted because while it improved sound projection on the other made the mouthpiece unequal and unmanageable in control.
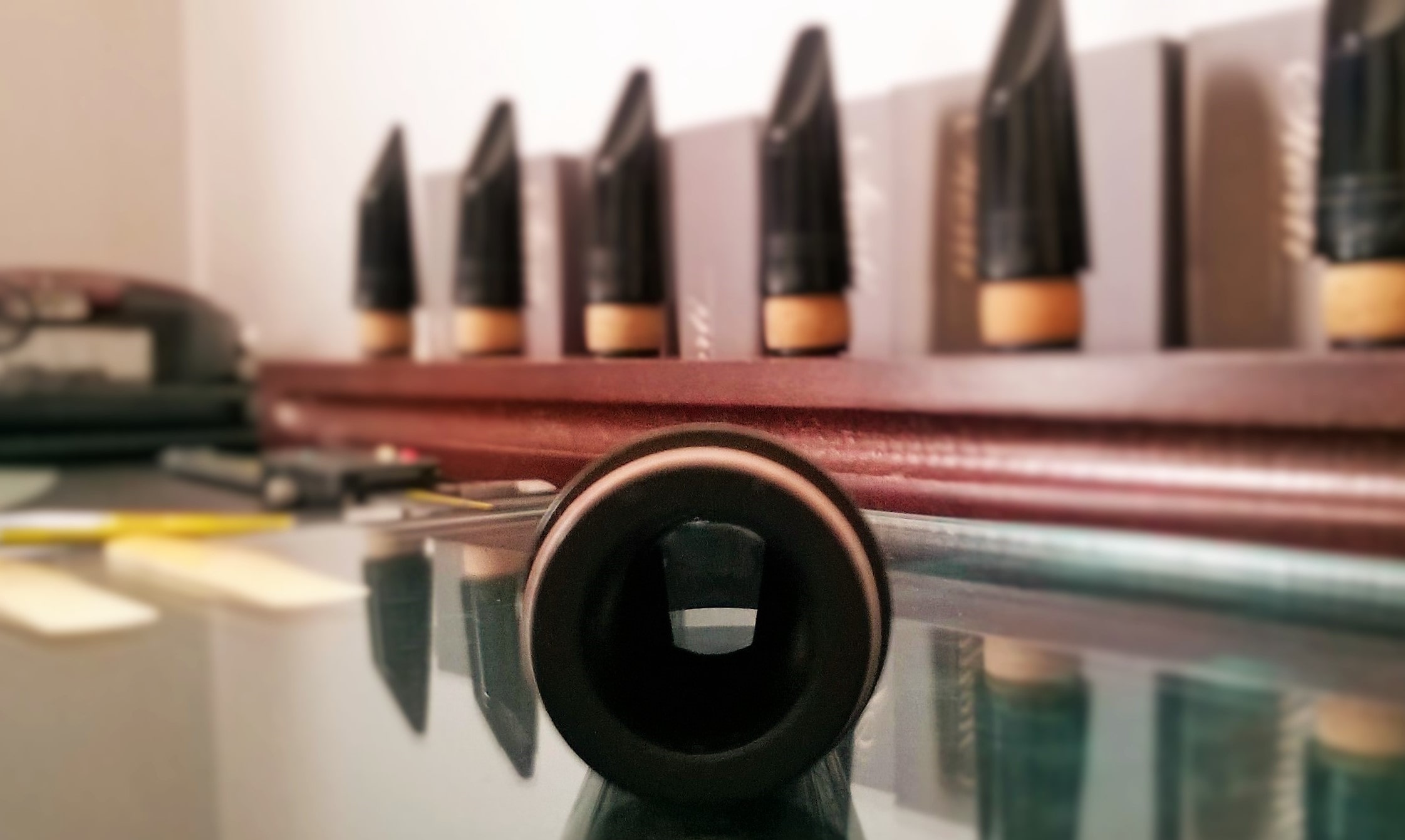
Today, thanks to the technology and the development of new techniques of construction we are able to re-propose some solutions abandoned in the past, obtaining mouthpieces with great projection that maintain an exceptional equality between the registers, ease of attack and excellent control of the sound.
A form that had been abandoned, surely one of the most obvious even for the less experienced, is the inner chamber V, or, as it was called in the past, to A reversed; the majority of historical mouthpieces of the ‘900 they adopted this room, then slowly around 1950/60, the A has become an H: the inner sides slowly have become increasingly parallel //.
For this reason I share my models into two broad categories, one with inner chamber V and the other H, represented in my case from the parallel symbol //.

The Hard Rubber is the material more appreciated by craftsmen and artists, easy to work either by machine or by hand, it produces a burnished sound, warm and capable of great flexibility and tonal color.
There are different compounds, indifferent to moisture but not to the temperature, and especially not all with the same stamp and the same vibrations.
The natural rubber vulcanization (addition of a few percent sulfur to rubber tree latex, followed by heating) was discovered around 1840. In the beginning they used only natural rubber, but already in 1930 started adding accelerators and synthetic rubber to the mixture, then, indeed, in 1970 the Environmetal Protection Agency order to produce hard rubber with much less sulfur than the percentages used by mid-century. All this allows us to understand the great changes that have taken the mouthpieces of hard Hubber over time and why today it is not possible to reproduce the same mix of Chedeville, Kaspar, Selmer … built with the highest quality of rubber.
Hans Zinner says that the hard rubber of its blanks consists of natural rubber with a very close compound that used by Chediville; and actually working a mouthpiece with sandpaper, you notice a yellowish color, which I have not encountered in other blanks.
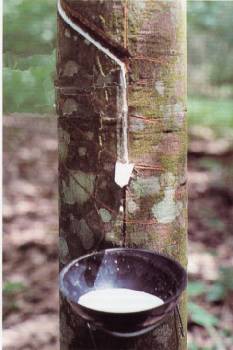
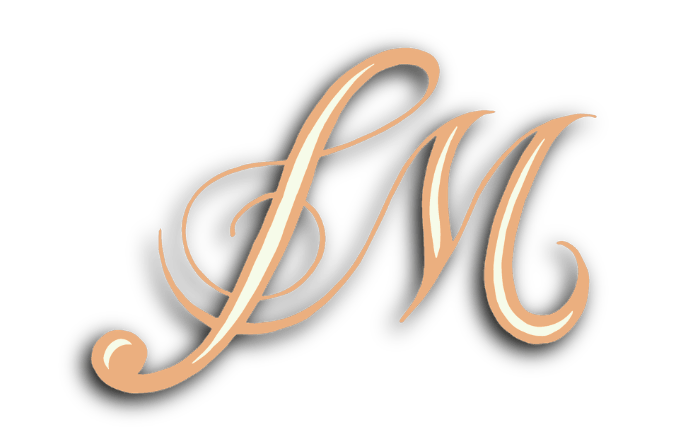
Mattia Storti – Via Nazionale, 237 – Cappone di Vallefoglia 61022 (PU) – Italia
P.Iva 02495490415 – C.F. STRMTT82M04L500B – Tel. +39 349 24 51 482 – stortimattia@yahoo.it – www.storticlarinetmouthpiece.com
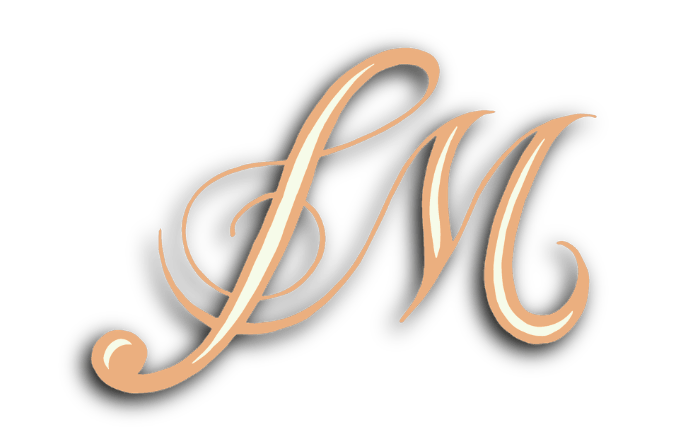